Introduction Of TSTC Automatic Revolving Doors
About the automatic revolving doors, electronic parts are necessary for the normal running. To TSTC Automatic revolving doors, our key parts including the main control unit,inverter, gearbox, radars, and the introduction for these parts will be showed as below .
* Main Control Unit
To the Main Control Unit, we used the 1st class system in the world, SIEMENS PLC, with a powerful intelligent I/O "positioning" module that was developed specially for installation in the programmable controller. It could provides numerous functions for both open-loop and closed-loop positioning. These functions are described in detail in the section entitled Modes. SIEMENS PLC could provide modes for positioning, coordinate shift and correction (compensation) All modes can be used both separately and as a consequence of individual functions in machining programs. The complex open-loop and closed-loop procedures which a standard programmable controller must perform in order to carry out a positioning task require a great deal of processor time. The IP 266 can considerably reduce the amount of processor time needed because it takes over the entire positioning process. Your control program can thus execute in parallel with the positioning procedure. Sequences of motions involving several axes are made possible by the use of additional modules.
* Inverter
Lenze Inverter is the one which we use most for our revolving doors, series AC Inverter for 0.25kW (0.33HP) 220V 3 Ph motor. Converts fixed frequency single phase 220V input to variable frequency three phase 220V to control the speed of a standard AC Induction motor. Operates in standard VxF or Sensorless Vector mode up 1.7A with 150% Overload.
Output rating : to 1.7A .
Overload: 150% x 60 seconds; 200% x 3 seconds.
Size A: 60mm Wide x 130mm Deep x 183mm High. IP20.
Weight: 0.8kg.
Speed Control Range: 0-599Hz
Braking: No Dynamic Braking
Input Current: 4A
Input Voltage: 200-240V Single Phase ±10% at 50-60Hz ±5% .
EMC Compliance: IEC 61800-3 Second Environment C2 (Industrial).
* Gearbox
SEWDRIVE Gearbox is the one which we use most for our revolving doors,the strength of SEW Gear Units is their simple mechanical structure. This yields a higher efficiency than pure worm gear units. In addition, the S series gear units are quiet during operation.The simple design makes the individual adjustment of torque and speed allows for space-saving installation ,however,the combination with a helical gear stage significantly increases the efficiency compared to pure helical-worm gear units. The torque ranges from 92 Nm to 4,000 Nm.
* Radars
Brand : BEA .
Technology : passive infrared and microprocessor
Optical characteristics: P.I.R. with 4 elements, 15 lenses with full independent masking possibilities .
Maximum Detection area (mounting height: 2.2m): 2.5 m (W) x 1.5 m (D)
Minimum Detection area (mounting height: 2.2 m) : 0.5 m (W) x 0.5 m (D)
Detection mode: motion .
Detection speed: 0.1 to 1.5 m/s .
Light indicator: 1 red LED: flashes for a few seconds after power-on .
Hold time: 0.5s ou 2s .
Response time: < 200 ms .
Recommended cable section (terminal block):< 0.5 mm² .
Standard output:relay (free potential contact) .
Mounting height: 3m max .
Temperature range: from -30 °C to +55 °C .
Conformity: EN 61000-6-2; EN 61000-6-3; EN 50581 .
* Key Switch
The revolving door could be able to be set to operate in one of the following modes as required by the building owner. The switching between these modes is turn of a key on an operating panel.
Lock: The door can find locking-up position automatically and lock up manually to ensure safety of the whole building.
Continous revolving: Door keep revolving at low speed if no pedestrians, door revolves at normal speed if pedestrians are detected by infrared sensor and the
mode will keep on until no pedestrians. Specially designed for heavy traffic flow.
Go-stop: the door will automatically revolve (through sensor activation) when the door is approached upon. This setting is ideal to reduce energy consumption.
* Encoder
Topydic series small shaft incremental encoder EL40AX6 delivers outstanding performance in mechanical shock-resistance and is capable of withstanding higher axial and radial loads so as to meet various industrial environments. Its special position of cabling fits to the limited space. Combining advanced signal processing technology with multiple types of electrical output, EL40AX6 are capable of matching various upper control computers.
Protection class: IP66 .
Max. Speed rpm: 6000 rpm 1, continuous .
Max. load capacity of the shaft : 60 N axial, 100 N radial.
Output circuit: RS422, Push-Pull .
Materials: Shaft stainless steel .Housing Al-Zn-alloy .
Vibration resistance: 10G/10 - 2000 Hz .
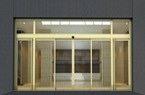
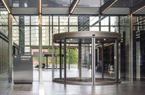
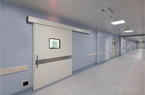
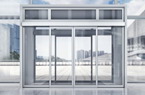